Quick and Reliable Product Packaging Device Repair Service Services to Lessen Downtime
In the competitive landscape of production, the effectiveness of packaging procedures pivots on the integrity of machinery. Quick and reliable fixing solutions are essential in reducing downtime, which can lead to considerable operational troubles and economic losses.
Significance of Timely Repair Works
Prompt repair services of product packaging devices are important for keeping functional performance and reducing downtime. In the fast-paced atmosphere of manufacturing and packaging, even minor malfunctions can result in considerable delays and performance losses. Resolving problems quickly makes certain that makers operate at their optimal ability, thus guarding the flow of procedures.
Furthermore, prompt and normal upkeep can avoid the rise of minor issues right into significant malfunctions, which often sustain higher repair costs and longer downtimes. A positive strategy to machine fixing not only maintains the stability of the equipment but also improves the general reliability of the assembly line.
Furthermore, timely repair services add to the longevity of packaging equipment. Machines that are serviced immediately are less most likely to deal with extreme deterioration, enabling businesses to optimize their investments. This is especially essential in industries where high-speed product packaging is essential, as the requirement for regular performance is paramount.
Benefits of Reliable Service Carriers
Dependable service suppliers play a critical function in making certain the smooth operation of packaging makers. Their know-how not just enhances the efficiency of fixings yet also adds significantly to the long life of devices.
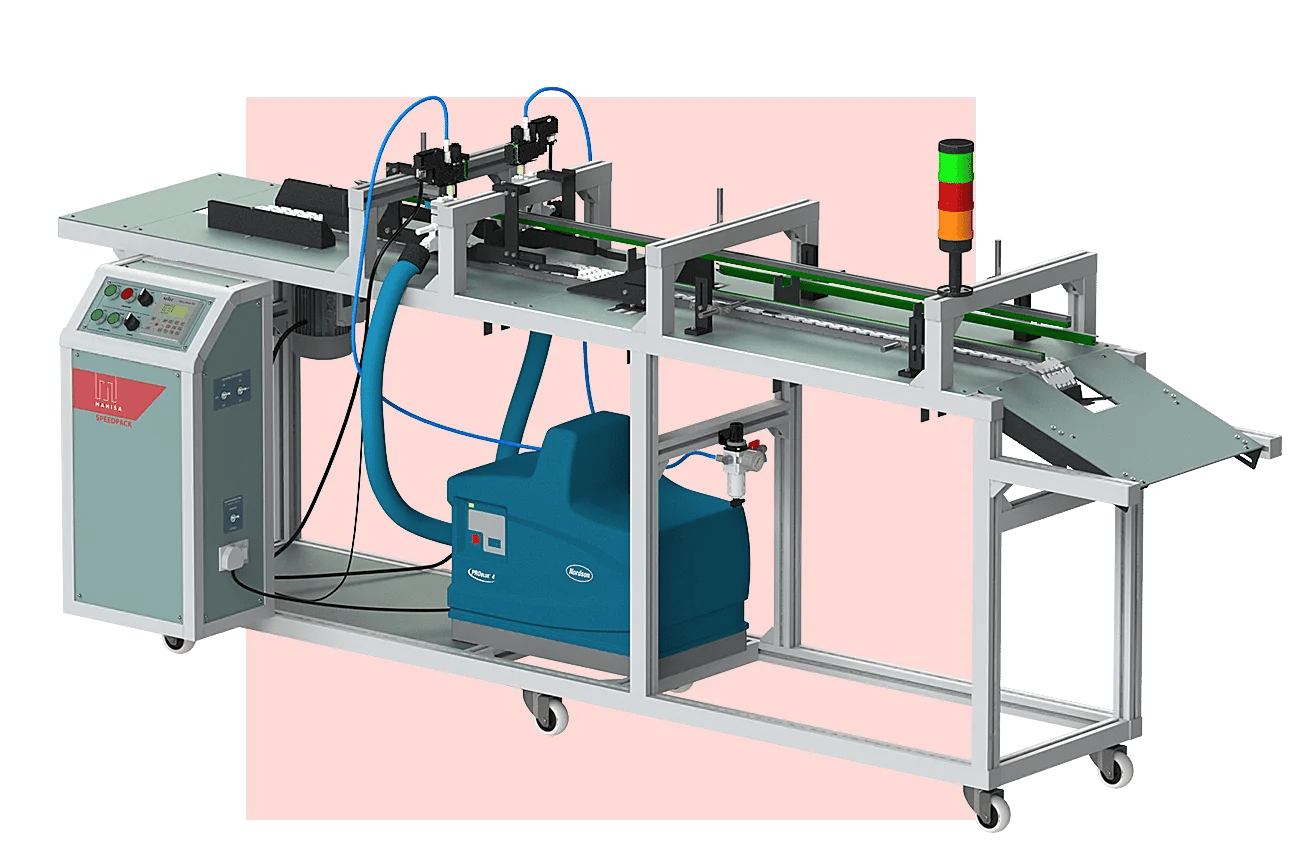
Additionally, a trustworthy solution copyright provides extensive support, including training and support for team on machine procedure and upkeep ideal practices. This not just encourages employees however additionally cultivates a culture of safety and security and efficiency within the organization. In general, the advantages of engaging dependable service companies expand past immediate repairs, positively impacting the whole functional workflow of product packaging procedures.
Common Product Packaging Device Concerns
In the world of packaging operations, different problems can compromise the effectiveness and capability of equipments (packaging machine repair). Another typical concern is imbalance, which can create jams and uneven product packaging, affecting item high quality and throughput.
Electrical issues can likewise interrupt packaging procedures. Damaged electrical wiring or malfunctioning sensing units might cause unpredictable maker behavior, causing hold-ups and increased operational prices. In addition, software program glitches can prevent the machine's shows, leading to functional ineffectiveness.
Irregular product circulation is another critical issue. This can emerge from variants in item dimension, form, or weight, which might influence the maker's capacity to take care of things precisely. Not enough training of operators can intensify these problems, as untrained personnel might not recognize early signs of malfunction or might misuse the devices.
Resolving these usual product packaging machine concerns without delay is important to preserving performance and ensuring a smooth operation. Regular inspections and positive maintenance can dramatically reduce these concerns, promoting a trustworthy product packaging environment.
Tips for Decreasing Downtime
To decrease downtime in packaging procedures, implementing a proactive upkeep method is critical. Regularly scheduled upkeep checks can identify prospective issues before they escalate, guaranteeing devices operate effectively. Developing a regimen that consists of lubrication, calibration, and examination of vital elements can dramatically lower the frequency of unanticipated malfunctions.
Training team to operate equipment properly and recognize early warning signs of breakdown can likewise play an important duty. Equipping operators with the understanding to perform basic troubleshooting can protect against minor issues from creating significant delays. Additionally, maintaining an efficient inventory of crucial spare components can quicken repairs, as waiting on parts can bring about extended downtime.
Additionally, documenting machine performance and upkeep tasks can assist determine patterns and recurring issues, permitting targeted interventions. Including innovative monitoring innovations can give real-time information, making it possible for predictive maintenance and reducing the risk of sudden failures.
Finally, fostering open communication in between drivers and maintenance groups makes sure that any type of irregularities are quickly reported and addressed. By taking these proactive actions, companies can boost functional performance and considerably minimize downtime in product packaging procedures.
Selecting the Right Repair Service Service
Picking the ideal repair work solution for product packaging equipments is an important decision that can considerably impact operational effectiveness. Begin by examining the provider's experience with your specific kind of product packaging tools.
Next, take into consideration the provider's reputation. Seeking click here now comments from other businesses within your sector can give insights into dependability and top quality. Certifications and partnerships with acknowledged equipment producers can additionally show a commitment to quality.
Furthermore, examine their feedback time and availability. A provider that can provide prompt support reduces downtime and maintains manufacturing circulation consistent. It's also essential to ask about guarantee and solution assurances, which can mirror the self-confidence the provider has in their work.
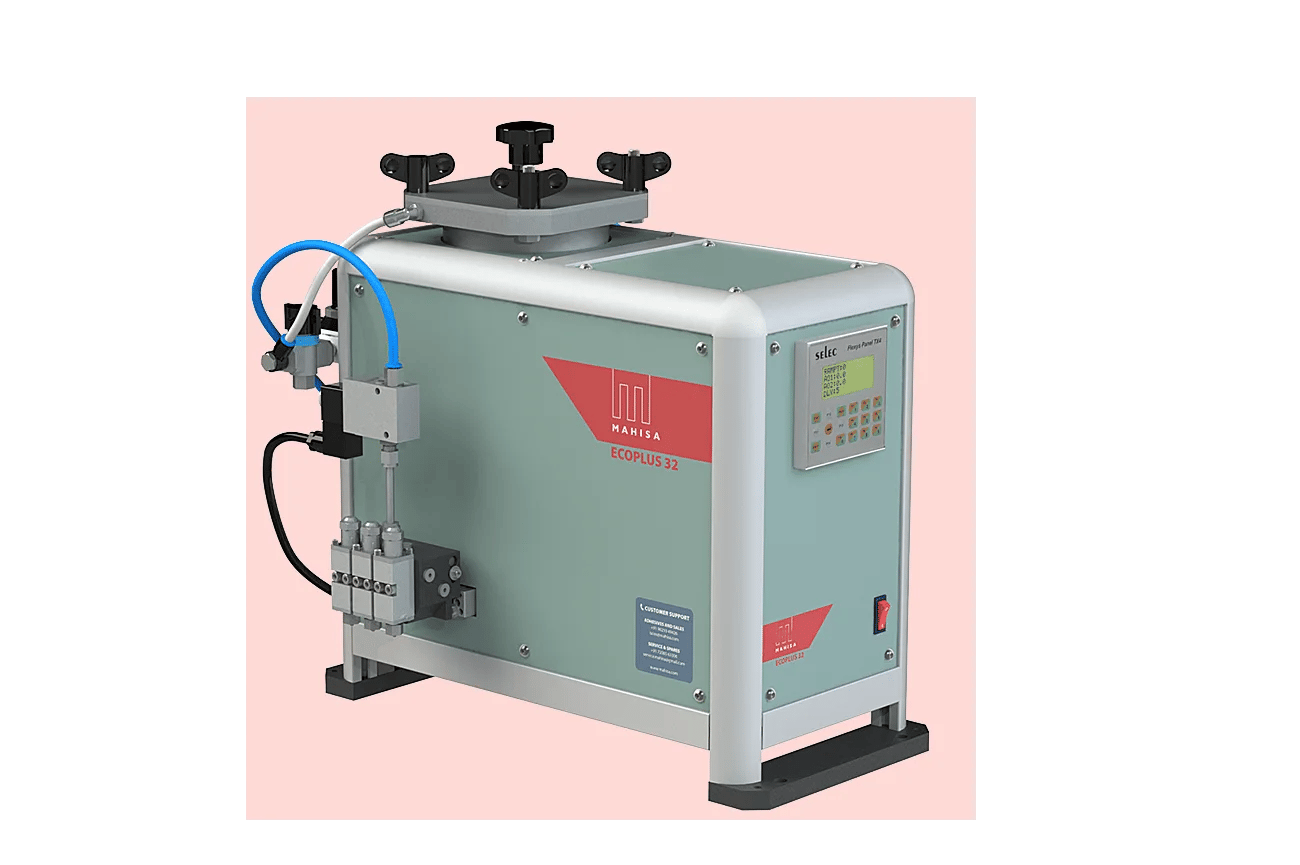
Verdict
Finally, the value of trustworthy and fast product packaging maker repair solutions can not be overemphasized, as they play an important function in reducing downtime and making sure operational efficiency. By prioritizing prompt repair services and selecting reliable provider, companies can successfully keep and deal with common problems efficiency. Executing positive upkeep methods and investing in staff training further boosts the longevity of product packaging machinery. Ultimately, a critical method to repair solutions fosters a much here are the findings more resilient production setting.
Timely repairs of product packaging machines are important for maintaining operational efficiency and decreasing downtime.In addition, timely check my site fixings add to the longevity of packaging machinery. Generally, the benefits of engaging reliable solution companies expand past instant repair services, positively influencing the whole functional workflow of product packaging procedures.
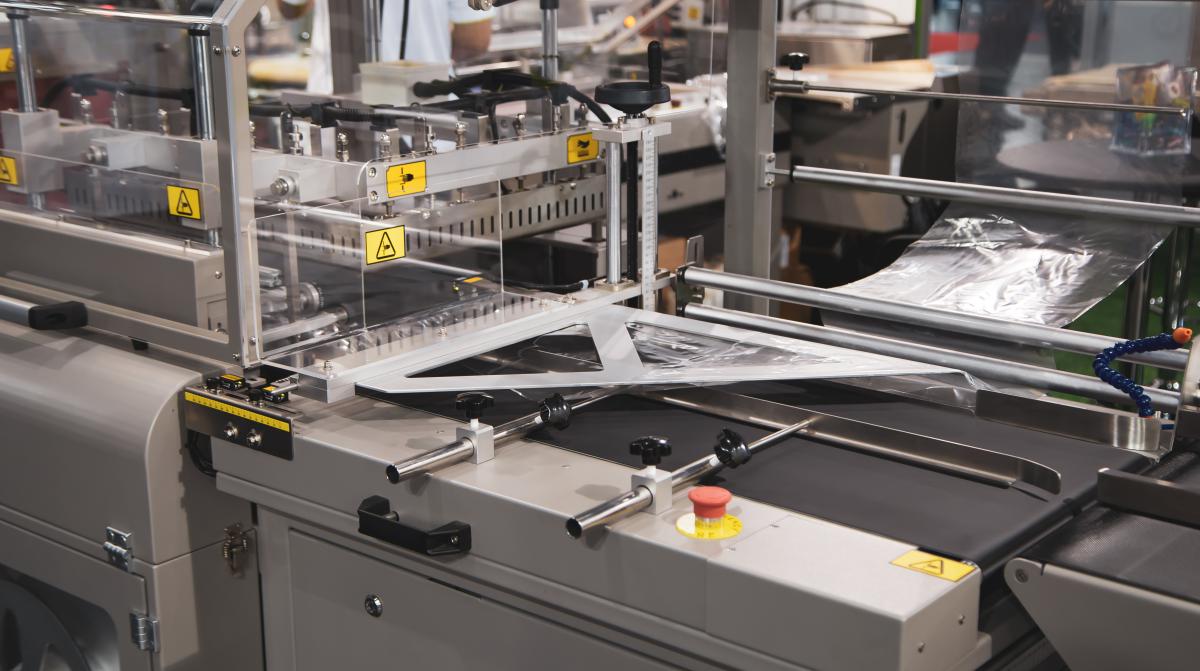